Manufacturing Process
Although most antibiotics occur in nature, they are not normally available in the quantities necessary for large-scale production
For this reason, a fermentation process was developed. It involves isolating a desired microorganism, fueling growth of the culture
and refining and isolating the final antibiotic product. It is important that sterile conditions be maintained throughout the manufacturing
process, because contamination by foreign microbes will ruin the fermentation
Starting the culture
- Fermentation can begin, the desired antibiotic-producing organism must be isolated and its numbers must be
increased by many times. To do this, a starter culture from a sample of previously isolated, cold-stored organisms is
created in the lab. In order to grow the initial culture, a sample of the organism is transferred to an agar-containing
plate. The initial culture is then put into shake flasks along with food and other nutrients necessary for growth. This
creates a suspension, which can be transferred to seed tanks for further growth.
- The seed tanks are steel tanks designed to provide an ideal environment for growing microorganisms. They are filled
with the all the things the specific microorganism would need to survive and thrive, including warm water and carbohydrate
foods like lactose or glucose sugars. Additionally, they contain other necessary carbon sources, such as acetic acid, alcohols,
or hydrocarbons, and nitrogen sources like ammonia salts. Growth factors like vitamins, amino acids, and minor nutrients round
out the composition of the seed tank contents. The seed tanks are equipped with mixers, which keep the growth medium moving, and
a pump to deliver sterilized, filtered air. After about 24-28 hours, the material in the seed tanks is transferred to the primary fermentation tanks.
Fermentation
- The fermentation tank is essentially a larger version of the steel, seed tank, which is able to hold about 30,000 gallons.
It is filled with the same growth media found in the seed tank and also provides an environment inducive to growth. Here the microorganisms are
allowed to grow and multiply. During this process, they excrete large quantities of the desired antibiotic. The tanks are cooled to keep the
temperature between 73-81° F (23-27.2 ° C). It is constantly agitated, and a continuous stream of sterilized air is pumped into it. For this reason,
anti-foaming agents are periodically added. Since pH control is vital for optimal growth, acids or bases are added to the tank as necessary.
Isolation and purification
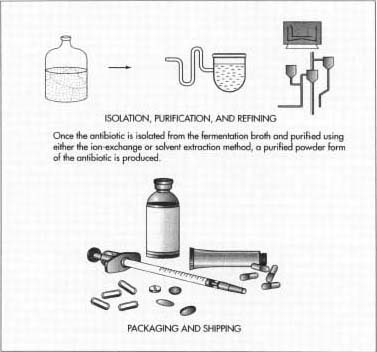
- After three to five days, the maximum amount of antibiotic will have been produced and the isolation process can begin.
Depending on the specific antibiotic produced, the fermentation broth is processed by various purification methods. For example,
for antibiotic compounds that are water soluble, an ion-exchange method may be used for purification. In this method, the compound
is first separated from the waste organic materials in the broth and then sent through equipment, which separates the other water-soluble
compounds from the desired one. To isolate an oil-soluble antibiotic such as penicillin, a solvent extraction method is used. In this method,
the broth is treated with organic solvents such as butyl acetate or methyl isobutyl ketone, which can specifically dissolve the antibiotic.
The dissolved antibiotic is then recovered using various organic chemical means. At the end of this step, the manufacturer is typically
left with a purified powdered form of the antibiotic, which can be further refined into different product types.
Refining
- Antibiotic products can take on many different forms. They can be sold in solutions for intravenous bags or syringes, in pill or
gel capsule form, or they may be sold as powders, which are incorporated into topical ointments. Depending on the final form of the
antibiotic, various refining steps may be taken after the initial isolation. For intravenous bags, the crystalline antibiotic can be
dissolved in a solution, put in the bag, which is then hermetically sealed. For gel capsules, the powdered antibiotic is physically
filled into the bottom half of a capsule then the top half is mechanically put in place. When used in topical ointments, the antibiotic
is mixed into the ointment.
- From this point, the antibiotic product is transported to the final packaging stations. Here, the products are stacked and put in
boxes. They are loaded up on trucks and transported to various distributors, hospitals, and pharmacies. The entire process of fermentation,
recovery, and processing can take anywhere from five to eight days.